Should you purchase a used kiln for annealing your beads? Here's a few random thoughts on the topic.
A kiln is not really any more sophisticated than a well-insulated toaster oven. Sometime you see older kilns for sale - here's some questions to ask before you buy:
What what is designed for, and what has it been used for? A quick google may find that out for you. Ceramics kilns, kilns for enameling, etc, all can be used, with some caveats. Kilns for metal clay are relatively new - so unlikely to be too old or damaged. These may be sorta small - but they might work. Enamelling kilns may have some messy spills inside - but you can put a kiln shelf over it if you can't get the stuff out.
What voltage is it? 220 or 110. 110 is easy - 220 is faster to heat up and more efficient, but you have to have the plug for it (like a dryer plug.) Installing a 220 volt plug is non-trivial - it requires an electrician.
Are the elements encased? Bead kilns often have the heating elements in quartz tubes - this prevents you from touching them accidentally with metal mandrels. Metal mandrel on metal element is a bad thing. Alternately - the elements in a bead kiln may be recessed in the roof of the kiln where they are harder to stick a mandrel into. (But, not impossible. I know of someone who has done this.)
Top opening or front opening? A door on the front is nice - and if it has one - will it stay up by itself? Top opening - I know quite a few bead makers that prefer this. A pair of long tweezers helps a lot - put on the big suede welding gloves, grasp the mandrel below the bead with the tweezers, swing the door open (now you are losing heat) - pop the bead in, and swing it closed. You can practice with the kiln off and just mandrels!
How big is the inside of the kiln? Mandrels are often 9 inches or 12. Do you have enough room to get the mandrels in? Or, conversely - is it so big it is overkill? Heating that extra space will cost money.
How big is the outside of the kiln? You need space around it between it and the walls, etc. Do you have room for it? (Hint - if it takes more than one strong person to move it - it's probably overkill for beads.)
Is it old? It may be quite inefficient and leak heat through old, damaged firebricks or a poorly-fitting door. Ceramic fibre blanket can be replaced, however - especially around doors - where I think it is designed to be replaced on a regular basis. If the clips to hold this in place are missing - a couple of bent mandrels can replace them. Bend to shape. I use bent mandrels to repair all manner of things!
Are the elements in good shape? - not sagging or heavily corroded or kinked? Elements can be replaced - but they ain't free. Might be worth it though.
Is is controlled by a kiln-sitter? Ceramic kilns have a device that uses a cone melting at a specific temperature to shut off the kiln (called a kiln sitter) - a rather ingenious method of controlling the temperature but not accurate enough for glass. The usual protocol is to circumvent the cone sitter and install a pyrometer (a thermometer for high temperatures) to display the temperature and to manually control the temp with the control dial, or to install a digital controller. (Installing a digital controller is easy, btw. There is usually a hole in the kiln for the temperature probe. Pull this out - they aren't usually secured. Thread the one from the controller into the hold. Plug the kiln into the controller. Plug the controller into the wall. Turn the kiln to full. Set the controller. That's it. Done.)
If it's a very good price - it may be a good deal. (To me - I would want it to be under $200). Otherwise - kilns have come down a lot - and I do love having a digital controller! And a swing up bead door!
Of course - check out the cost of shipping if it isn't local - that may destroy any savings you were going to get!
Pages
▼
Thursday, April 30, 2009
Wednesday, April 22, 2009
Happy Hour Torching
Announcing - Happy Hour Torching
Starting this Thursday - April 23rd - Happy Hour Torching at beadFX. Torch one hour - get the second hour free. 5 til 9 p.m.
I've found that - while it is wonderful to sit down in your own studio and make beads - it can also be a lot of fun to do with other lampworkers around - you can get a really cool energy going and lots of great ideas pop out.
beadFX is the studio where I teach. They also rent studio time, by the hour or in blocks of time (by the hour, $15/hour or a block of 10 hours is $12/hour - which you can use up in increments as small as 15 minutes.) Torch time includes annealing - dipped mandrels, use of basic tools and glasses, and the beads being pulled for you the next day (which, on some days, I feel is worth the cost alone!). Glass is available for purchase, or bring your own.
So the deal is: Torch for one hour, either on a studio card or at the hourly rate - and get the second hour free. (No credits, must use free hour immediately - i.e. no saving it up for later.)
I'll be in the studio also torching from 7 - 9 at least - possibly earlier - so if you have questions or need help with a technique - you can fire away with the questions! Or you can just fire away!
Come out and bead social! (Calling or emailing the store to reserve a torch might be wise!)
Update on Abby: I'm hoping to bring her home the end of this week! She's not walking or standing yet - but she is getting movement back in her legs. Her arthritis is very bad - which makes getting her moving harder - but critical!
Friday, April 17, 2009
Still Here

I rushed her to emerg (it was Good Friday, remember?) and they diagnosed a ruptured disc between L1 and L2.
She had surgery on Monday. She's still at the clinic - and I'm visiting her every day. This has taken up a lot of my energy.
I haven't gone away - I just have nothing particularly glassy to say - except - I need to sell a lot of beads.
Wednesday, April 08, 2009
TAG 104 - Taxco Light Limited Edition
The two spacers are very lightly reduced. Not much going on - but a pretty colour regardless.
The bicone in this pic has been reduced a little more - but still - very light reduction. A soft, bushy flame, rather than a strong reduction flame. You can see a bit more effect.
The cylinder bead is over white - and the Taxco appears to have fumed the white - making it look more yellow.
There is more of an iridescence on this bead - but it's darn hard to shoot!
This one - I was quite pleased with the amount of iridescence I got. This is black and ivory, encased in Taxco Light. Really nice oil-slick sheen. Again - really light reduction.
And finally - over dichro. Because, d--- it - eventually I put everything with dichro!
Tuesday, April 07, 2009
TAG 104 - Green Dalai
Green Dalai - an experimental or limited edition batch from TAG. I decided to treat it like the Dalai - i.e. "heat the snot out of it, and strike it."
The first bead, on the left, I super heated and made the bead, and just let it cool. While it was hot - it had a lot of colour - and so I just popped it into the kiln. It came out really dark - the colour is there - but you need an insane amount of light to see it.
This second bead, I did the same - superheated it, allowed it to cool all the way to not glowing - and then struck twice in the flame. Although, while it was hot - it looked pretty much the same as the above bead, and it didn't look much different while striking - now that it is out of the kiln - I am much happier with this one. Apols for the poor focus - but this pic shows the colours the best.
Third version - my working notes say:
- snot
- cool
- encase
- mash
- really hot
Really like the streaky blues and greens! I might like this better than the regular Dalai Lama!
Monday, April 06, 2009
Yum! Lined beads
So far - I'm just enjoying lining single colour "spacers." The red one is 26 mm outside diameter - the lined hole is 8.4 mm.
The red is Lauscha Transparent Light Red (the batch that goes cloudy) and the blue one, on the left, is CiM Halong Bay.
I have a couple of observations - in no particular order, as yet.
If the tubing is too long for the hole - the result is much uglier than if it is too short. Err on the side of shorter. Too long, and it starts to collapse and turn into an oval hole!
You can easily anneal your tubing on your torch. Have a pot of water handy - slide your cut tube piece onto an undipped mandrel - hold level. (If you think you might tip your hand and slide the tube towards you - wrap a turn of glass around the mandrel to act as a stopper - you can crack or shock it off later - or use a bent mandrel.) Hold the tubing in the flame till it gets a dull red glow - take it out immediately (this is easier to see without too many lights on.) It will heat up very fast. Use a small flame - a little on the bushy side. I melted through the first two pieces of tubing. It goes very fast. When you get your dull red glow - slide into the water to cool.
A wire brush on a dremel is great for deburring after cutting the tubing.
I'll keep you posted as I get to larger and larger holes!
Sunday, April 05, 2009
Glass Craft Expo
Just got an excited call from a friend on the floor at the Glass Craft and Bead Expo - in Vegas. She was at the Invitational Hot Glass flame-off. To one side of her was Milon Townsend - building a 10 foot tall rocking chair - in glass. To the other side was Doni Hatz and her team - building a 3 foot tall bird cage - with birds. Further down, Bandhu Scott Dunham is building a glass replica of the mousetrap from the game - with a dichro marble being made to roll down it - being made by ... now I forget.
Damn. Shoulda gone.
Damn. Shoulda gone.
Wednesday, April 01, 2009
Saturday Lampworkers Get Together, Nortel Bead Liner

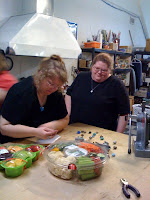
Thanks to Erin and Jen for the photos of the people who were there!


Anyway - great time was had by all. We have these get togethers once a month or so, and rotate around local studios and also go to restaurants, etc. If you want to be informed about the next one, you can subscribe to the mailing list or find the Toronto Lampworkers group on Facebook!
